CNC Machining for High-Temperature Applications
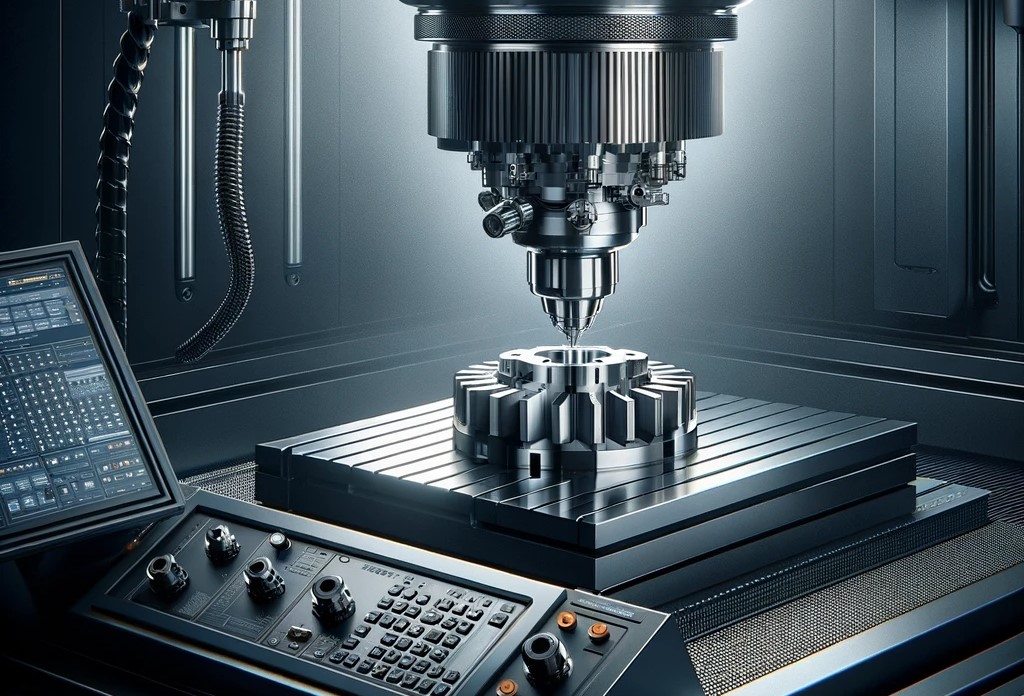
As we push the boundaries of technology and engineering, the demand for components that can withstand extreme conditions has soared. High-temperature applications, in particular, present a unique set of challenges and opportunities. Enter CNC (Computer Numerical Control) machining – a technology that has become synonymous with precision manufacturing. Yet, when it comes to materials like Inconel that thrive in high-temperature environments, CNC machining ventures into a domain where only the most advanced and innovative techniques can ensure success.
Challenges in Machining High-Temperature Materials
Overview of High-Temperature Materials
Materials like Inconel, a family of nickel-chromium-based superalloys, are renowned for their exceptional strength and resistance to extreme temperatures and corrosion. These properties make them indispensable in sectors that demand reliability under stress, such as aerospace for jet engines, the energy sector for turbine blades, and the automotive industry for exhaust systems.
However, the very attributes that make these materials invaluable also make them a formidable challenge to machines. The high strength of Inconel, for instance, results in significant tool wear and, consequently, a need for frequent tool replacement, impacting both cost and production time.
Specific Machining Challenges
The main challenges in machining high-temperature materials include:
- Tool Wear: The hardness and abrasiveness of materials like Inconel lead to accelerated wear and tear on cutting tools, reducing their lifespan.
- Material Toughness: These materials’ toughness requires higher machining forces, increasing the strain on CNC machines and potentially leading to inaccuracies in the final product.
- Heat Management: The efficiency of heat dissipation is lower in high-temperature materials, raising the risk of damaging both the workpiece and the tool during machining.
- Surface Finish and Precision: Achieving a high-quality surface finish and maintaining precision is more challenging due to the material’s properties and the stresses placed on tools.
Solutions and Innovations in CNC Machining
As the demand for precision and efficiency in manufacturing continues to rise, the field of CNC machining is evolving rapidly. Innovations in machine technology, cutting materials, and operational strategies are crucial to staying ahead in a competitive industry. This section delves into the latest advancements that are shaping the future of CNC machining. From enhanced tool materials that offer superior durability and heat resistance, to adaptive machining strategies that optimize performance in real-time, and groundbreaking cooling techniques that prevent thermal damage, we explore how these developments are not only enhancing the capabilities of CNC machines but also revolutionizing the manufacturing process. Each subsection provides an in-depth look at these innovations, highlighting their benefits and applications in today’s industrial landscape.
Advanced Tool Materials and Coatings
The development of tool materials with higher temperature resistance and durability is a key innovation in machining high-temperature materials. Tools coated with materials like titanium aluminum nitride (TiAlN) can withstand higher temperatures, reducing wear and extending tool life.
Adaptive Machining Strategies
Cooling Techniques and Lubricants
Aerospace Application - Jet Engine Components

One of the most demanding applications for high-temperature materials is in the aerospace industry, particularly in the manufacturing of jet engine components. These components must withstand extreme temperatures and pressures, making materials like Inconel the material of choice due to their heat resistance and strength.
Challenge: The primary challenge in machining jet engine components is maintaining precision and integrity in parts that must endure high temperatures and stresses. The toughness of Inconel results in significant tool wear, increasing production costs and time.
Solution: Through the adoption of advanced tool materials and coatings, combined with adaptive machining strategies, manufacturers have significantly improved the machining process. Tools coated with titanium aluminum nitride (TiAlN), for instance, can withstand the high temperatures generated during machining, reducing wear and extending tool life. Additionally, adaptive machining strategies optimize machining parameters in real time, ensuring precision while minimizing tool damage.
Impact: These technological advancements have not only improved the efficiency and cost-effectiveness of producing jet engine components but also enhanced the performance and reliability of the engines themselves. This is crucial for the aerospace industry, where safety and performance are paramount.
The Future of CNC Machining for High-Temperature Applications
Emerging Trends and Technologies
- Smart CNC Machining: The integration of IoT (Internet of Things) and AI (Artificial Intelligence) into CNC machines is transforming manufacturing. Smart CNC machines can predict tool wear, automatically adjust parameters for optimal performance, and even anticipate potential machining issues before they occur. This predictive maintenance and optimization significantly reduce downtime and enhance production efficiency, especially critical in machining high-temperature materials where precision and tool condition are paramount.
- Advanced Cooling Techniques: Innovations in cooling methods, including cryogenic machining and minimum quantity lubrication (MQL), are set to become more prevalent. These technologies not only improve tool life and surface finish but also contribute to the sustainability of manufacturing processes by reducing the use of coolants and minimizing waste.
- Ultra-Precision Machining: As the demand for precision continues to escalate, especially in sectors like semiconductor manufacturing and optics, the development of ultra-precision CNC machining techniques becomes crucial. These methods are capable of achieving nanometer-level accuracy, opening up new possibilities for manufacturing components with stringent tolerance requirements.
Elevating Customer Experience through Technology
In an era where customer expectations are higher than ever, leveraging technology to enhance customer experience becomes a competitive advantage. CNC machining companies can achieve this by:
- Utilizing AR (Augmented Reality) and VR (Virtual Reality) for immersive product demonstrations and prototyping.
- Implementing advanced e-commerce platforms and customer portals for streamlined ordering and tracking.
These technological touchpoints create a more engaging and informative customer journey, building loyalty and trust in the CNC machining brand.
Conclusion
The evolution of CNC machining in high-temperature applications reflects the remarkable strides made through technological innovation and industry collaboration. Advancements in this field demonstrate our collective commitment to pushing the boundaries of manufacturing excellence. Looking ahead, the future holds immense promise for further progress and mastery in machining high-temperature materials. As we continue to innovate and collaborate, we embark on an exciting journey towards a future where these complexities are not just managed but truly mastered.
On-demand CNC Machining Services by Ethereal Machines offers the perfect solution for your CNC machining needs. With secure and confidential processes, you can get an instant quote and access expert advice from their technical team. Whether you need custom CNC machined parts or have a specific project in mind, Ethereal Machines is committed to helping you every step of the way. Try MAAS now and achieve your goals with ease.
Views: 489