Advanced Cooling Techniques in High-Speed CNC Machining
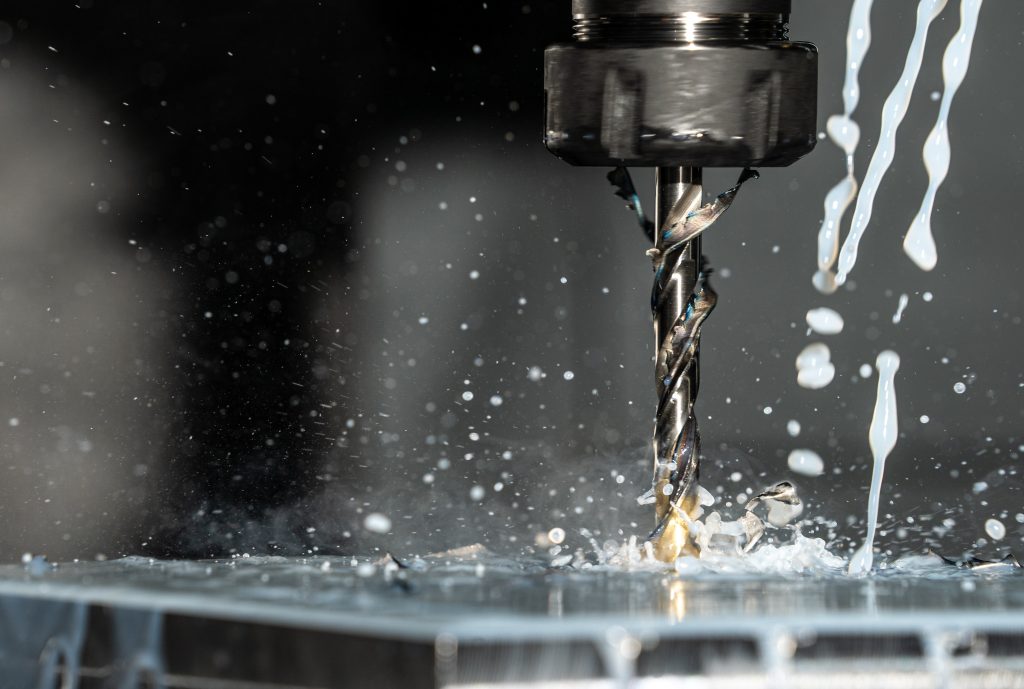
In the highly specialized field of CNC machining, precision and efficiency are paramount. Industries such as aerospace and automotive continually push the limits of what is possible, making the management of machining temperatures increasingly critical. Advanced cooling techniques are not merely enhancing; they are transforming high-speed CNC operations. This article explores the cutting edge of cooling technology, including Cryogenic Cooling, High-Pressure Coolant (HPC) Systems, and Minimum Quantity Lubrication (MQL). Each of these systems offers unique benefits aimed at optimizing manufacturing processes. We will delve into the specifics of how these systems operate, and the remarkable benefits they deliver, and provide examples of real-world applications that demonstrate their transformative impacts.
The Significance of Cooling in CNC Machining

Challenges of High-Speed CNC Machining
High-speed CNC machining presents a dynamic landscape where the generation of heat is both rapid and intense. This environment puts traditional cooling methods to the test, often surpassing their capacity to manage temperature effectively. The implications of overheating are significant, affecting not only the durability of the machining tools but also the dimensional accuracy and surface integrity of the machined parts.
The precision demanded in aerospace engineering and medical device manufacturing leaves little room for error. Thermal distortion, a common consequence of inadequate cooling, can render parts unusable, failing to meet the stringent specifications required. Moreover, the accelerated tool wear not only increases operational costs but also impacts production timelines, posing challenges to efficiency and profitability.
Innovations in Cooling Techniques
Notes:
- Ratings are based on the most common outcomes observed in industry studies; specific results may vary based on machine type, material, and operating conditions.
- LN2 = Liquid Nitrogen, MQL = Minimum Quantity Lubrication, HPC = High-Pressure Coolant.
- Sustainability considerations include the entire lifecycle impact of the lubrication/cooling strategy.
- Tool life extension is compared to traditional flood coolant systems.
- The regulatory compliance row reflects the typical industry burden but may differ by region.
Cryogenic Cooling
This technique leverages the extreme cooling effects of liquid nitrogen or CO2. By directly targeting the cutting zone, cryogenic cooling can significantly reduce temperatures without the need for large volumes of coolant. Its precision and efficiency make it an ideal match for high-speed machining, although considerations for handling and equipment adaptation are necessary.
Benefits of Cryogenic Cooling
- Superior Tool Longevity: Studies indicate that cryogenic cooling can extend tool life by up to 50% compared to conventional methods. This is achieved by minimizing thermal stresses that lead to premature tool wear.
- Enhanced Surface Integrity: By maintaining lower stable temperatures, cryogenic cooling prevents metallurgical distortions and maintains the geometric accuracy of the workpiece, crucial for industries like aerospace where precision is paramount.
- Efficient Material Removal: Cryogenic cooling is particularly effective with hard-to-machine materials such as Inconel and titanium, commonly used in the aerospace and medical industries. The rapid cooling allows for faster cutting speeds without the risk of heat-induced damage.
- Reduced Environmental Impact: By using minimal amounts of coolant, cryogenic cooling aligns with sustainable manufacturing practices, significantly reducing hazardous waste and the need for coolant disposal.
Challenges and Considerations
- Cost of Implementation: The initial setup for a cryogenic cooling system involves a substantial investment in specialized equipment and retrofitting existing CNC machines, which might be prohibitive for smaller operations.
- Operational Safety: Handling and storing liquid nitrogen or CO2 requires strict safety protocols to protect operators from severe cold burns and asphyxiation risks associated with gas displacement.
- Coolant Logistics: The supply chain for liquid nitrogen is not as robust as for more traditional coolants, which can pose challenges for continuous operation, especially in regions with limited access.
Minimum Quantity Lubrication (MQL)
Benefits of MQL
- Environmental Sustainability: MQL significantly lowers the volume of coolant used, reducing the need for disposal and minimizing the release of harmful chemicals into the environment. This aligns with the increasing regulatory and societal pressures for greener manufacturing practices.
- Enhanced Tool Performance: The aerosolized lubricant ensures optimal coverage with minimal waste, providing sufficient lubrication to reduce friction and wear on tools. This can lead to increased tool life and reduced operational costs.
- Improved Workpiece Quality: MQL helps maintain the integrity of the workpiece by reducing thermal distortions and providing cleaner machining operations, crucial for achieving high precision in industries such as electronics and medical.
- Cost Efficiency: By minimizing coolant use, MQL reduces both the direct costs associated with purchasing and disposing of coolants and the indirect costs related to coolant maintenance and storage.
Challenges and Considerations
- Technology Integration: Adopting MQL requires modifications to existing equipment and systems to handle the precise delivery of aerosolized lubricants, which can represent a significant upfront investment.
- Skill and Training Requirements: Operators must be adequately trained to adjust the flow and mixture of lubricants, which is critical for achieving the desired outcomes and maintaining safety standards.
- Material Compatibility: MQL may not be suitable for all machining operations, particularly those involving materials that require heavy-duty cooling. Selecting the right lubricants and correctly adjusting their application is essential for effectiveness.
High-Pressure Coolant (HPC) Systems:
Benefits of HPC
- Optimal Chip Evacuation: One of the standout benefits of HPC systems is their ability to flush out chips effectively from deep holes and complex geometries. This capability prevents the chips from interfering with the cutting process, thereby reducing tool wear and potential machine downtime.
- Improved Tool Life and Productivity: The direct and powerful application of coolant reduces the heat generated during machining, substantially prolonging tool life. Additionally, it allows for faster cutting speeds and feeds, directly enhancing productivity.
- Enhanced Surface Finish: By minimizing the thermal impact on the workpiece and ensuring consistent cooling, HPC systems help in achieving superior surface finishes, critical for manufacturing components with tight tolerances.
- Reduced Thermal Distortion: High-pressure coolant minimizes the heat-related expansion and distortion of workpieces, which is especially important in precision engineering applications.
Challenges and Considerations
- Increased Equipment and Maintenance Costs: The installation and upkeep of HPC systems involve higher costs due to the need for specialized pumps and filtration systems designed to handle high pressures.
- Complexity in Setup and Operation: Implementing HPC systems requires careful setup and regular maintenance to ensure that the high-pressure coolant is delivered effectively without causing equipment issues or safety hazards.
- Specificity of Application: While HPC is beneficial for specific tasks, especially those involving hard metals or complex parts, it may not be as cost-effective for simpler machining operations where standard cooling methods are sufficient.
Conclusion
As we advance further into the era of precision manufacturing, the evolution of cooling techniques in high-speed CNC machining is not merely a trend but a critical necessity. The adoption of advanced methods like cryogenic cooling, MQL, and HPC systems marks a significant leap toward achieving unparalleled precision, efficiency, and sustainability in production environments. With real-world applications in cutting-edge sectors demonstrating substantial improvements in tool life and product quality, these technologies underscore the industry’s shift towards more sophisticated and environmentally responsible manufacturing practices. As these innovative cooling techniques continue to evolve, they promise to not only meet but redefine the standards of modern manufacturing.
<span data-metadata=""><span data-metadata=""><span data-buffer="">MAAS
Machining As A Service
On-demand CNC Machining Services by Ethereal Machines offers the perfect solution for your CNC machining needs. With secure and confidential processes, you can get an instant quote and access expert advice from their technical team. Whether you need custom CNC machined parts or have a specific project in mind, Ethereal Machines is committed to helping you every step of the way. Try MAAS now and achieve your goals with ease.
Views: 821