Advancing CNC Efficiency: Innovative Toolpath Optimization Techniques

CNC machining is witnessing an unprecedented evolution, driven by advancements in technology and changing market demands. Emerging trends like the integration of AI and ML, increased automation, and the push towards greener manufacturing practices are redefining the boundaries of what’s possible in CNC machining.
In a market where precision and efficiency are paramount, optimization stands as the key differentiator. CNC toolpath optimization not only boosts productivity but also enhances the quality of output, providing a competitive edge in an increasingly demanding industry.
Advanced Toolpath Optimization Techniques
The advent of sophisticated optimization techniques marks a significant leap in CNC machining capabilities. By reducing cycle times and enhancing tool life, these techniques ensure optimal utilization of resources, making them indispensable in a modern CNC setup.
Artificial Intelligence (AI) and Machine Learning (ML) in Toolpath Optimization
AI and ML are at the forefront of revolutionizing CNC toolpath optimization. These technologies enable the development of smarter, more adaptive machining strategies, leading to significant gains in efficiency and precision.
a) Genetic Algorithms (GAs) and Simulated Annealing (SA)
GAs and SA bring a level of computational intelligence to CNC machining, enabling manufacturers to achieve greater efficiency and precision. While these concepts originate in computer science, their application in CNC machining is a perfect example of how interdisciplinary knowledge can lead to significant advancements in industrial practices.
Genetic Algorithms (GAs) in CNC Machining:
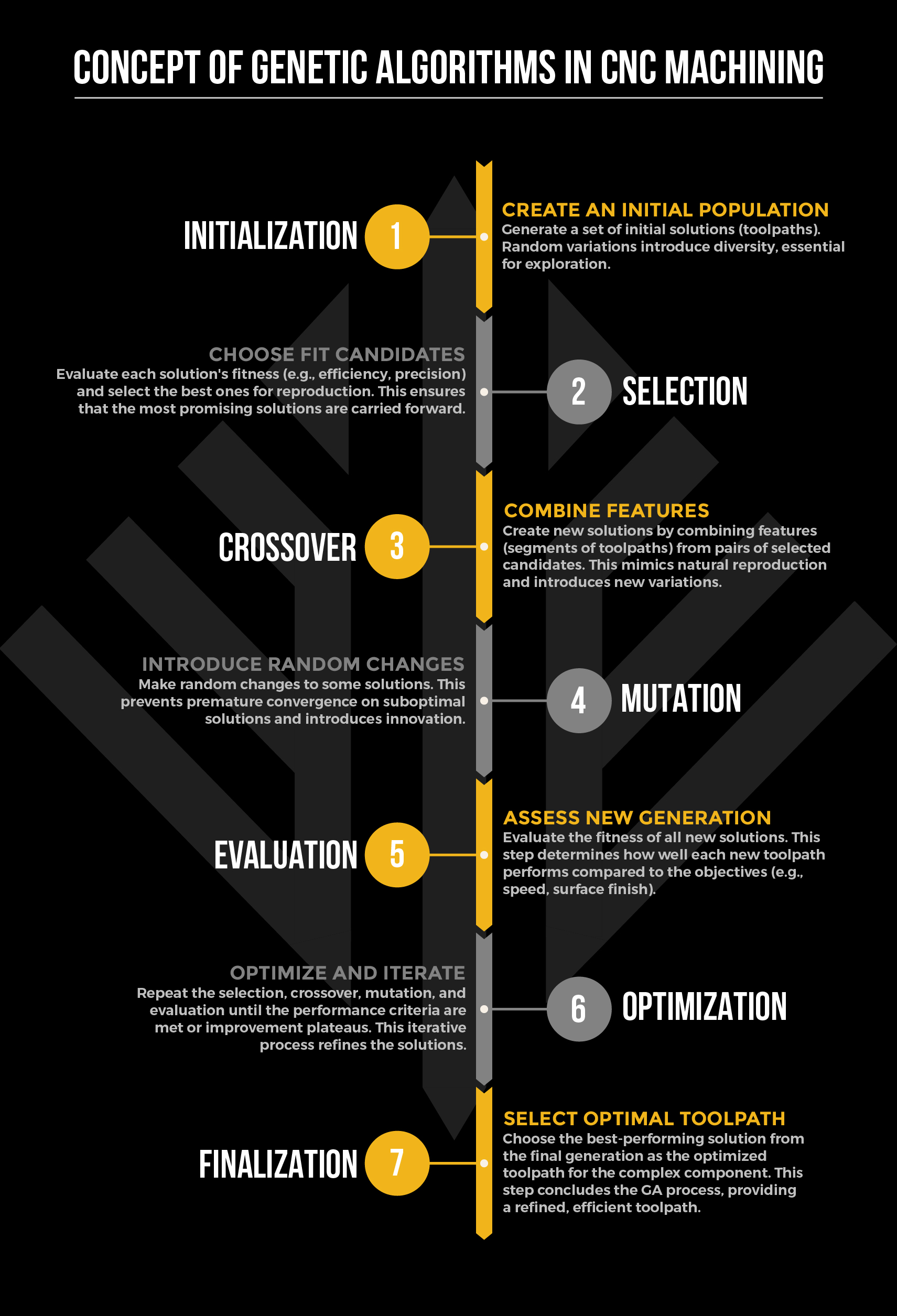
- Exploration of Solutions: In the context of CNC machining, GAs explore various possible toolpaths to find the most efficient one. Imagine having several different routes to machine a complex part. GAs will evaluate each route based on factors like time taken, tool wear, and quality of the finished product.
- Natural Selection: Just like in nature, where only the fittest survive and reproduce, GAs select the best toolpaths and combine elements of these paths to create new, potentially more efficient paths.
- Iterations: Over multiple iterations, or ‘generations,’ the algorithm keeps refining the toolpaths. With each generation, you get closer to the most efficient path for the CNC machine to take.
Simulated Annealing (SA) in CNC Machining:
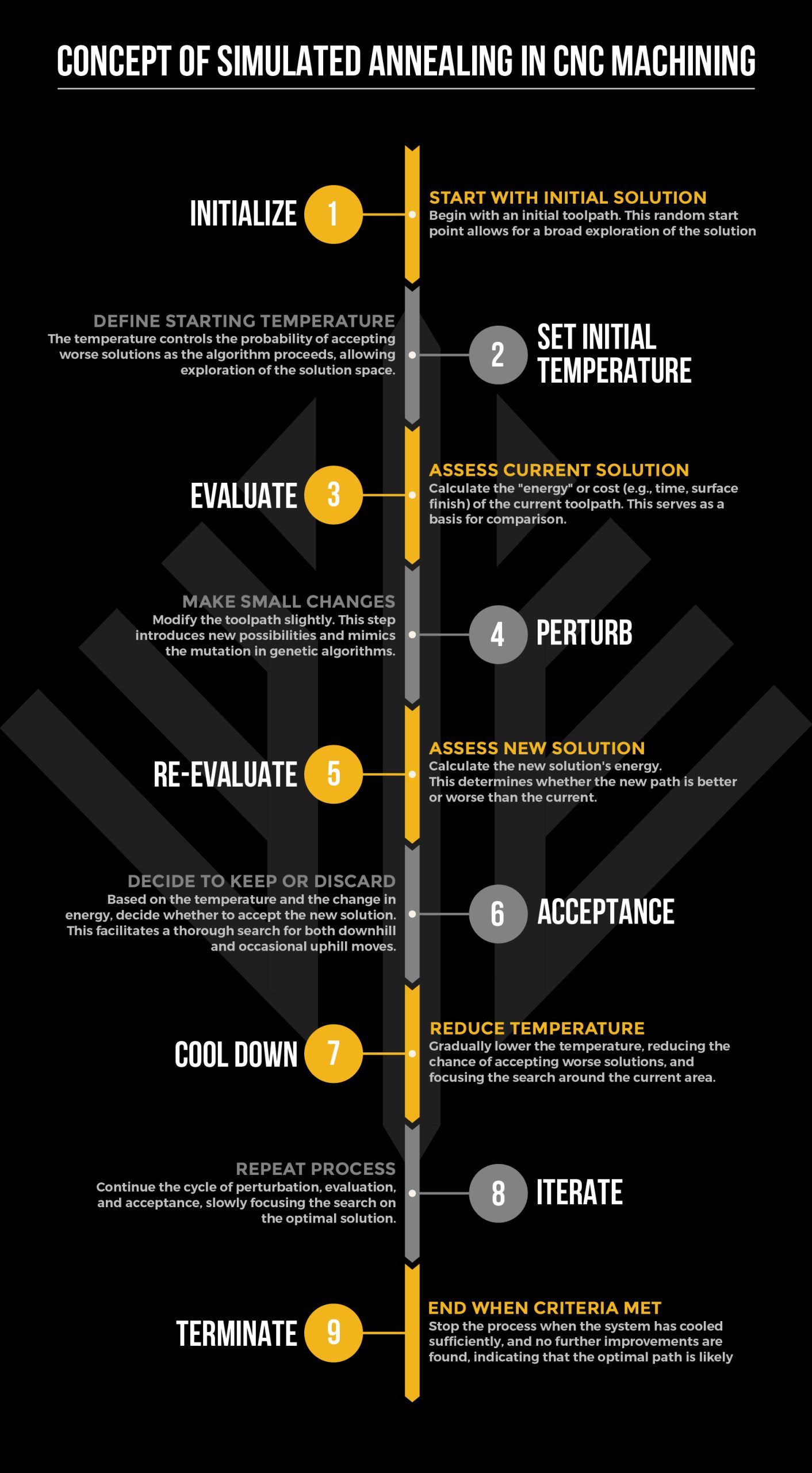
- Single Solution Refinement: Unlike GAs, SA starts with a single toolpath and makes incremental changes. Think of it like sculpting; you start with a rough shape and refine it gradually.
- Overcoming Local Optima: In CNC machining, it’s easy to get stuck in a ‘locally optimal’ toolpath that seems efficient but isn’t the best possible solution. SA overcomes this by allowing for occasional ‘jumps’ to explore new areas of the solution space, similar to heating a metal to make it malleable before it cools into a stronger form.
- Fine-tuning: As the ‘temperature’ lowers (a metaphor for the algorithm becoming more selective in its changes), SA fine-tunes the toolpath, making smaller adjustments to reach the most efficient path.
Practical Implications in CNC Machining:
- Efficiency and Quality: Both GAs and SA can significantly enhance the efficiency and quality of CNC machined parts. They ensure that the machine operates most effectively, reducing time and material waste.
- Complex Geometries: These algorithms are particularly valuable for complex or intricate parts where traditional toolpath planning might not be sufficient
b) Ant Colony Optimization (ACO) and Particle Swarm Optimization (PSO)
Ant Colony Optimization (ACO) in CNC Machining:
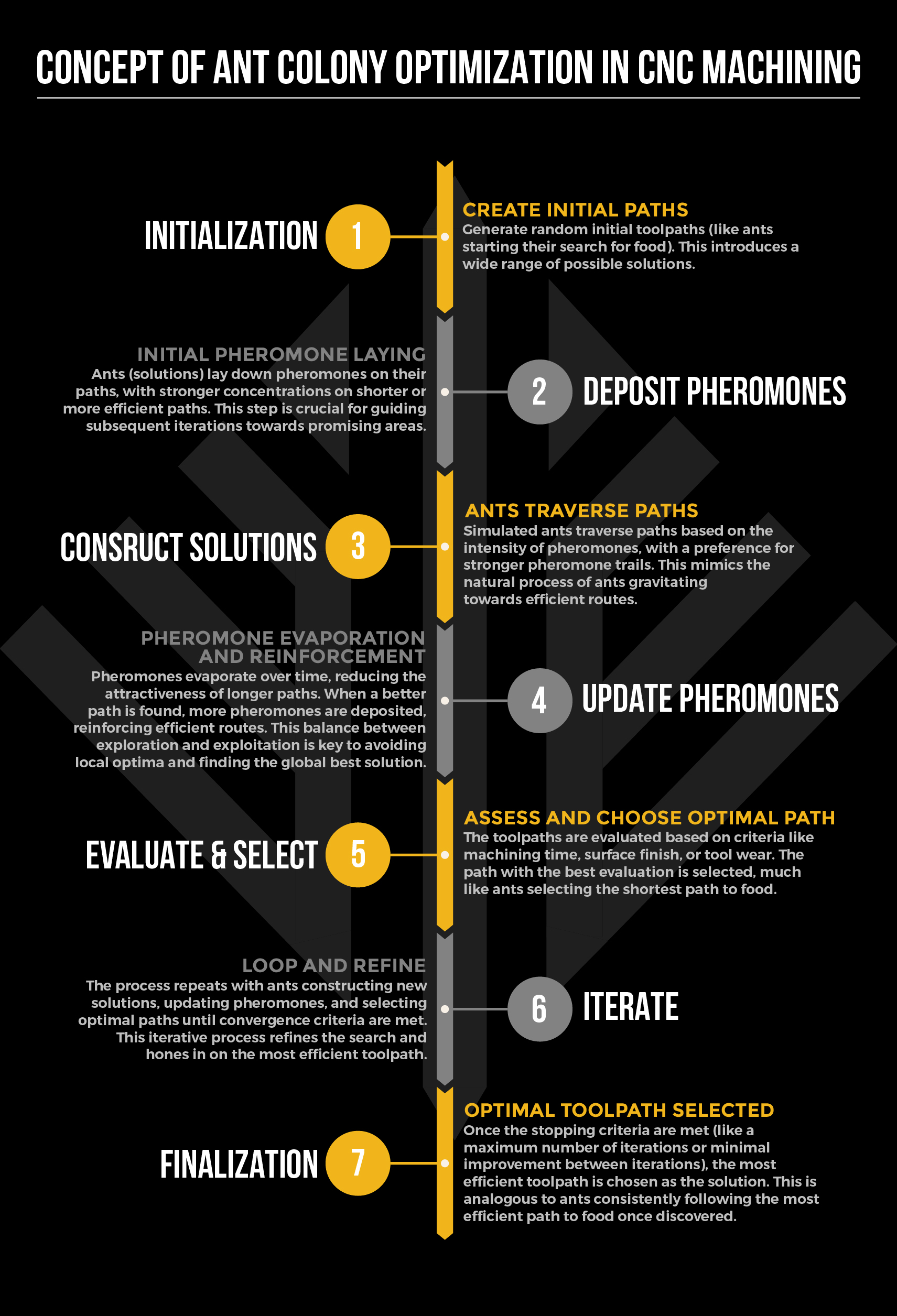
- Pheromone-Based Pathfinding: ACO algorithms simulate the behavior of ants laying down pheromone trails. In CNC machining, ‘virtual ants’ explore potential toolpaths, with more efficient routes accumulating stronger ‘pheromone’ signals, mimicking how ants find the shortest route to food.
- Iterative Optimization: Through multiple iterations, the ACO algorithm refines the toolpaths, leading to the emergence of the most efficient route for CNC machining, akin to ants optimizing their path to food.
- Efficiency in Complex Parts: Particularly effective for intricate or complex parts, ACO minimizes tool wear and reduces machining time, ensuring efficient and precise fabrication.
Particle Swarm Optimization (PSO) in CNC Machining:
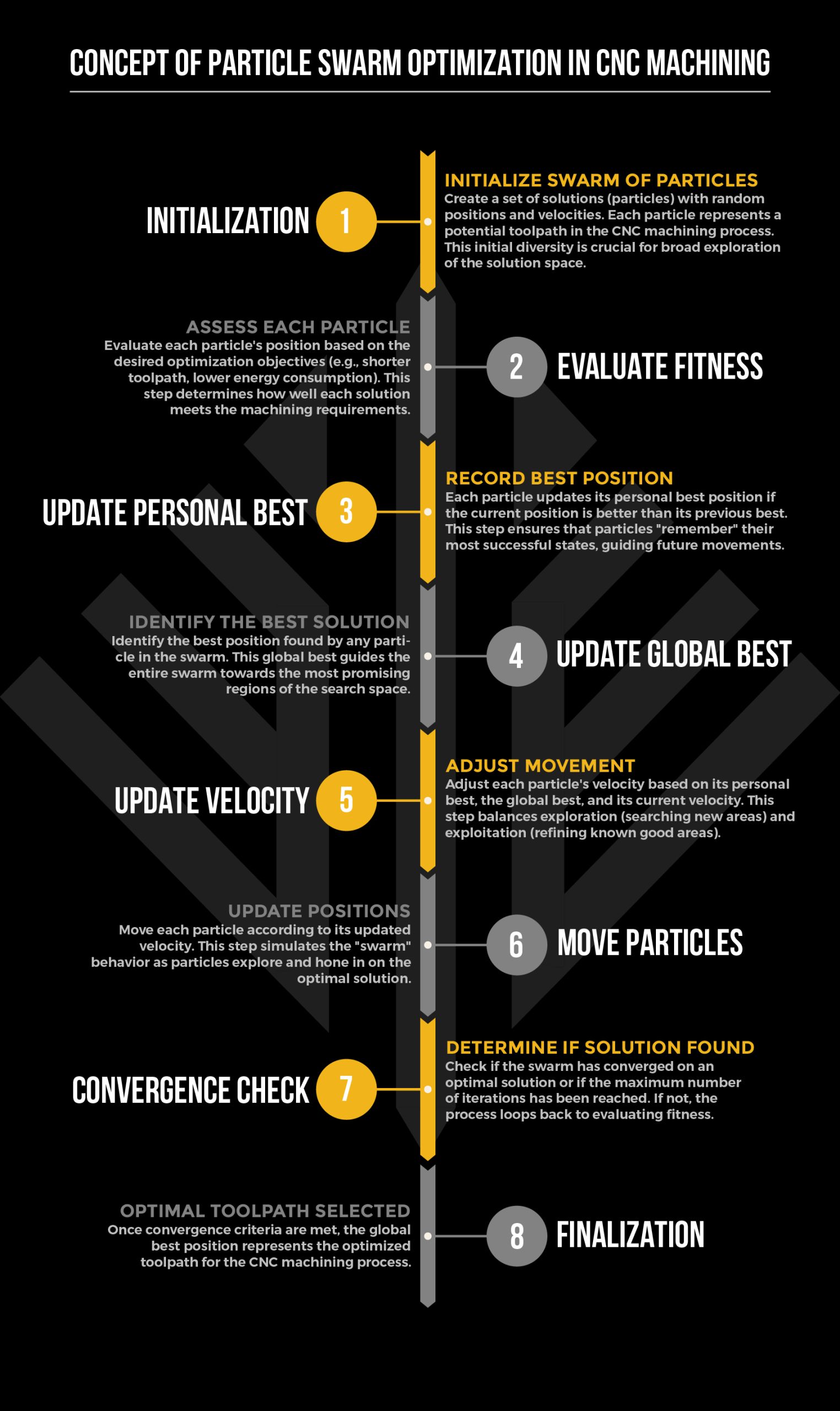
- Swarm Intelligence: Drawing inspiration from the social dynamics of bird flocks or fish schools, PSO models toolpath optimization as a process of social interaction within a swarm of ‘particles’ (potential solutions). Each particle adjusts its path based on its own experience and the success of its neighbors.
- Balance of Exploration and Exploitation: PSO excels in balancing exploration (searching new areas) and exploitation (refining known good solutions), much like a flock dynamically adjusting its flight pattern.
- Adaptability in Dynamic Environments: Suited for environments where operational parameters change, PSO quickly adapts, making it ideal for dynamic CNC machining scenarios.
Practical Implications in CNC Machining:
- Enhancing Efficiency and Precision: Both ACO and PSO offer new ways to optimize toolpaths in CNC machining, enhancing efficiency, reducing costs, and increasing precision.
- Interdisciplinary Innovation: The integration of these bio-inspired algorithms in CNC technology showcases the potential of combining fields for industrial innovation.
- Advancements and Impact: With ongoing developments in AI and machine learning, these algorithms are poised to further revolutionize smart manufacturing, cementing CNC technology’s role in industrial innovation.
c) Deep Learning and Reinforcement Learning for Adaptive Toolpath Planning
Deep Learning in CNC Machining:
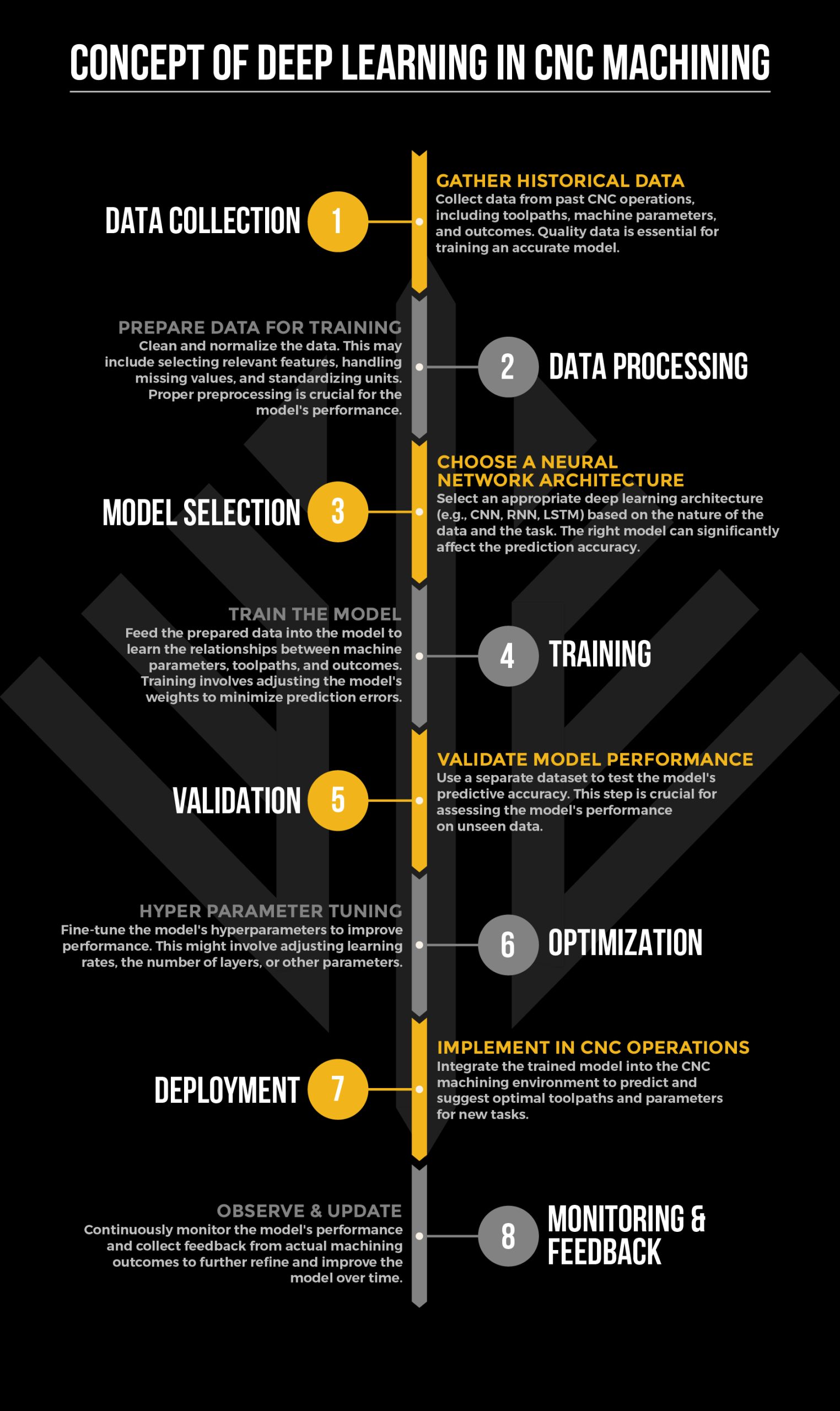
- Data-Driven Optimization: Deep learning algorithms use large datasets to learn and predict the most efficient toolpaths. By analyzing historical data on machining processes, these algorithms can identify patterns and make informed decisions about the best routes for machining different parts.
- Complex Problem Solving: These algorithms excel in handling complex, high-dimensional problems, allowing for intricate and precise toolpath planning in CNC machining. They can navigate through a myriad of variables such as tool geometry, material properties, and machining parameters to find the optimal path.
- Continuous Improvement: As more data is collected and analyzed, deep learning algorithms continually refine their predictions, leading to increasingly efficient and accurate toolpath planning over time.
Reinforcement Learning in CNC Machining:
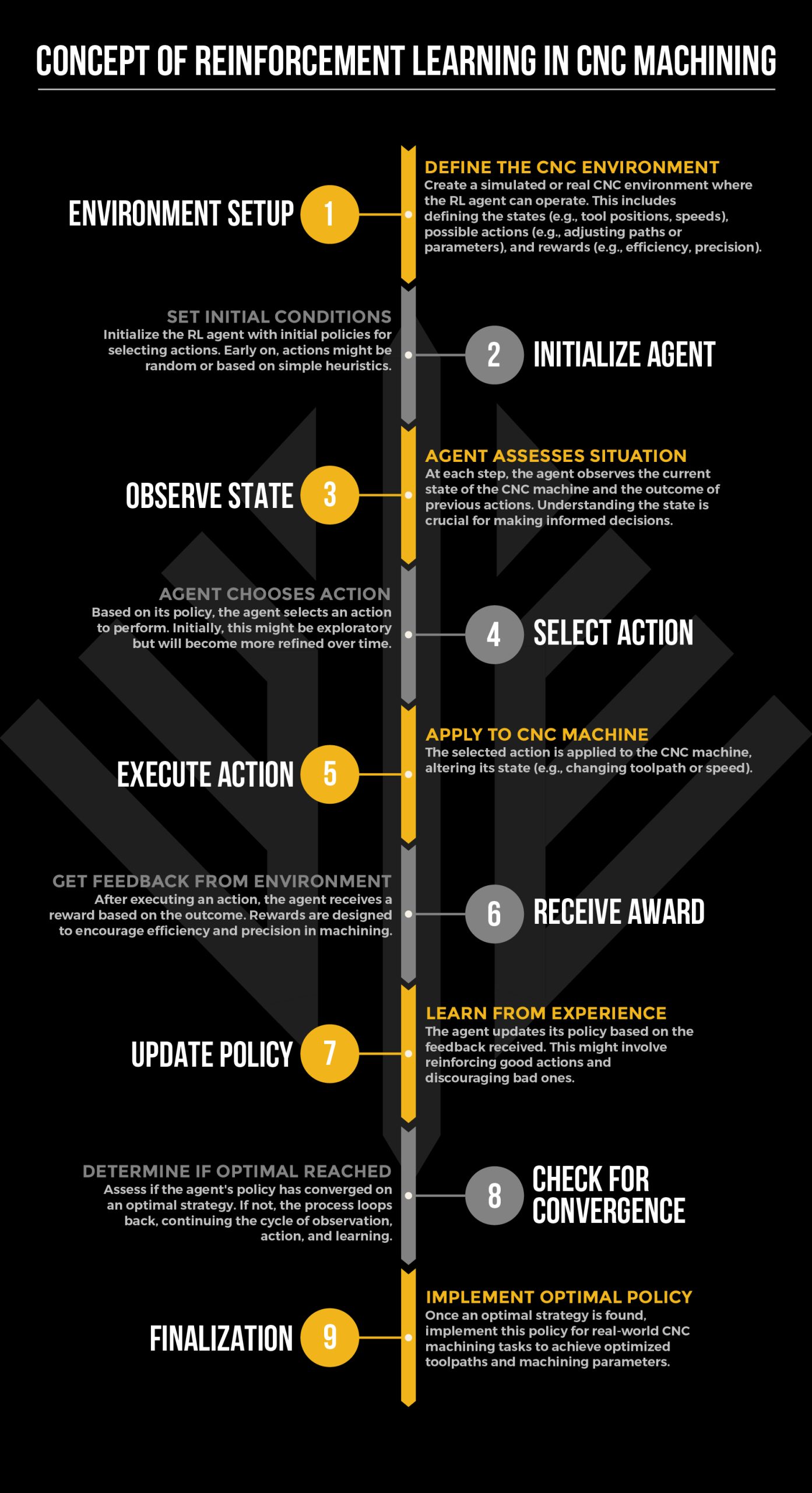
- Adaptive Decision Making: Reinforcement learning algorithms learn by interacting with the machining environment, constantly adjusting toolpaths based on real-time feedback. This allows for dynamic adaptation to changing conditions during the machining process.
- Goal-Oriented Optimization: Reinforcement learning focuses on achieving specific goals, such as minimizing tool wear, reducing machining time, or maximizing surface finish quality. The algorithm learns to balance these objectives to determine the best overall toolpath strategy.
Practical Implications in CNC Machining:
- Enhanced Machining Performance: The use of deep and reinforcement learning in CNC machining leads to more efficient, precise, and adaptive toolpath planning, ensuring optimal performance throughout the machining process.
- Future-Proofing CNC Technology: As these learning algorithms evolve, they offer potential for significant advancements in CNC machining, highlighting the importance of staying updated with these technologies for future industry developments.
- Interdisciplinary Innovation: The integration of advanced machine learning techniques in CNC technology represents a fusion of computer science and manufacturing, opening new avenues for innovation and efficiency in industrial processes.
Multi-Objective Optimization for Balancing Conflicting Goals
a) Optimizing for Machining Time, Surface Finish, and Tool Wear
Advanced Optimization in CNC Machining:
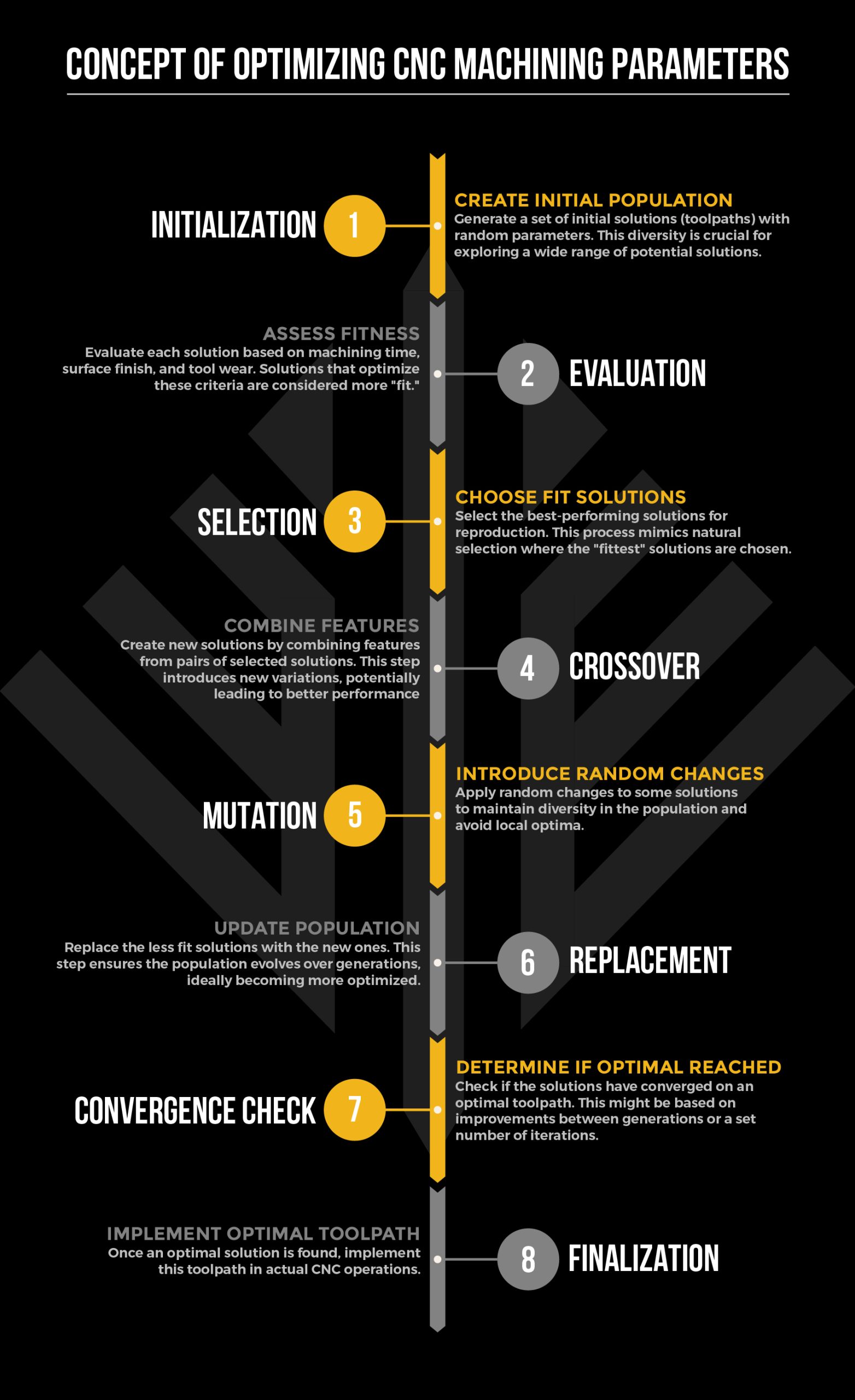
- Multi-Objective Optimization: These algorithms are designed to handle multiple objectives simultaneously, balancing the trade-offs between machining time, tool wear, and surface finish quality. This approach ensures that no single aspect is optimized at the expense of others, leading to a holistic improvement in CNC machining.
- Dynamic Balancing of Objectives: In CNC machining, factors such as machining time, tool wear, and surface finish often have competing requirements. Advanced optimization algorithms dynamically adjust priorities based on the specific machining context, ensuring the best possible outcome for each unique situation.
- Iterative Improvement: Similar to genetic algorithms, these advanced optimization techniques refine their solutions over multiple iterations. With each cycle, the algorithms learn from previous outcomes, steadily moving toward the optimal balance between machining time, tool longevity, and surface quality.
- Enhanced Production Efficiency: By optimizing for multiple objectives, these algorithms greatly enhance the efficiency of CNC machining processes, leading to faster production times without sacrificing quality or causing excessive tool wear.
- Adaptability to Complex Tasks: These algorithms are particularly useful in complex machining tasks where balancing different machining aspects is crucial. They can adapt to a wide range of materials, geometries, and machining conditions.
Practical Implications in CNC Machining:
- Raising the Bar for CNC Machining Standards: The use of advanced multi-objective optimization algorithms in CNC machining sets new standards for what can be achieved in terms of efficiency and quality.
- Driving Technological Innovation: The development and application of these algorithms encourage continuous technological innovation in CNC machining, pushing the boundaries of what is possible in digital fabrication.
- Strategic Advantage in Manufacturing: For manufacturing businesses, employing these advanced algorithms can provide a significant competitive advantage, enabling the production of high-quality parts at a lower cost and in less time.
b) Pareto-optimal Solutions and Trade-off Analysis
Pareto-Optimal Solutions in CNC Machining:
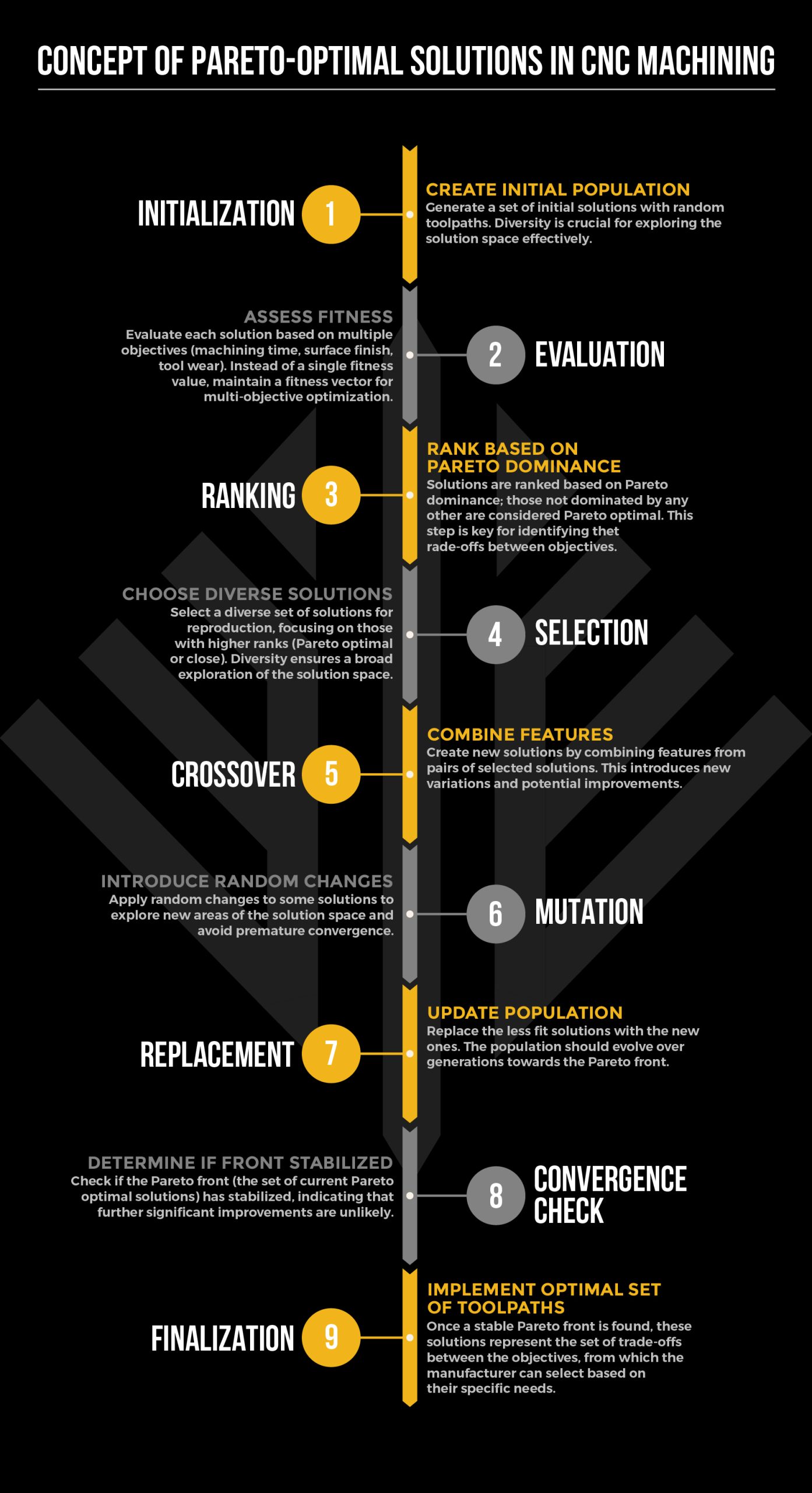
- Balancing Multiple Objectives: Pareto-optimal solutions involve finding the best possible balance among various machining objectives. In CNC machining, this could mean optimizing for factors like machining time, tool wear, surface finish, and energy consumption simultaneously.
- Set of Optimal Compromises: These solutions represent a set of trade-offs where improving one objective may lead to a decrease in another. Pareto-optimal solutions offer a range of options, each providing a different balance of these objectives.
- Efficient Decision Making: By considering Pareto-optimal solutions, CNC operators and engineers can make more informed decisions, selecting the toolpath that best meets the specific requirements of each machining task.
Trade-off Analysis in CNC Machining:
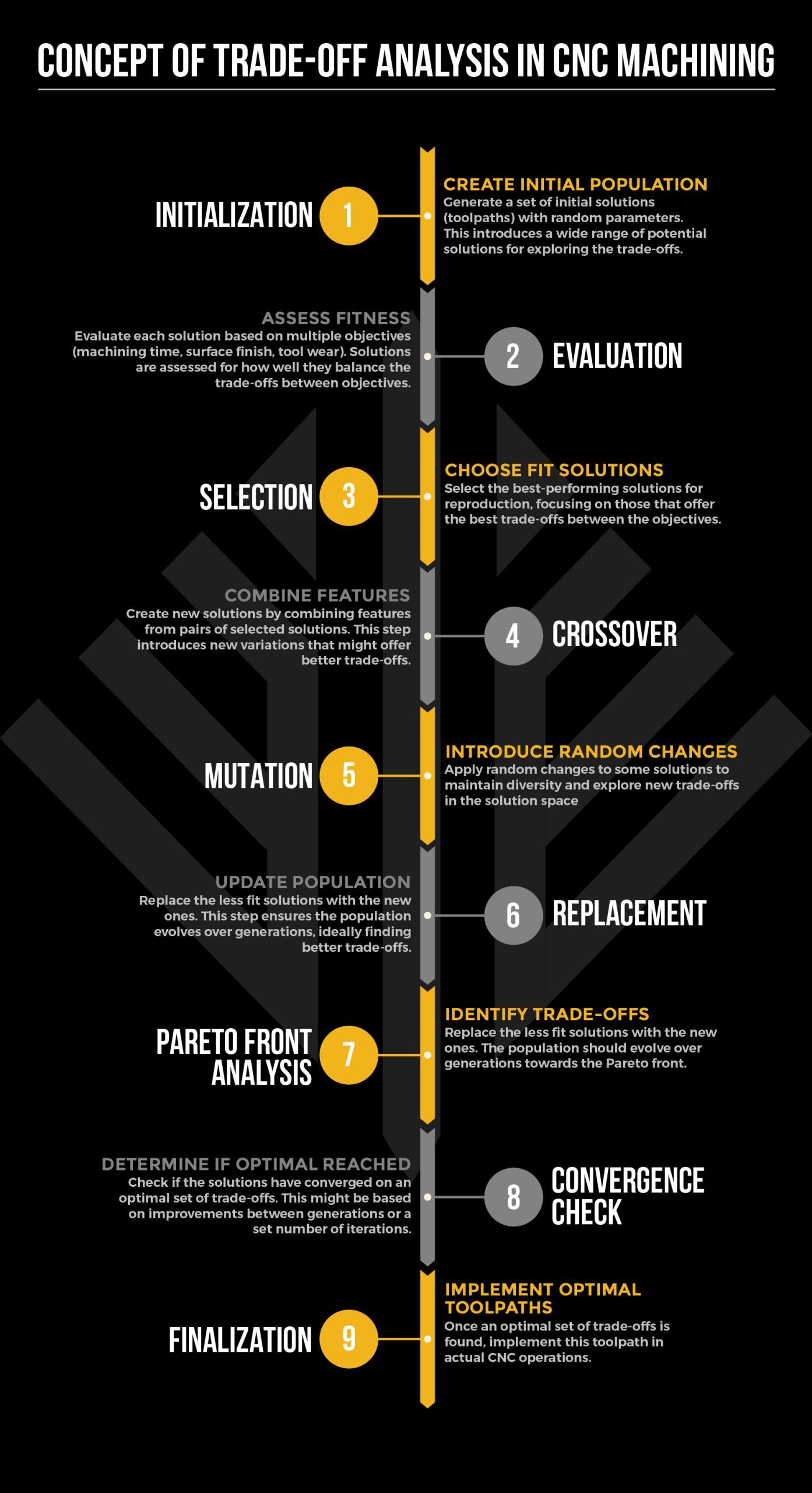
- Understanding Relationships between Objectives: Trade-off analysis helps in comprehending how different machining objectives affect each other. For instance, increasing speed might reduce machining time but could lead to greater tool wear or reduced surface quality.
- Choosing the Best Solution: Through trade-off analysis, engineers can identify the most suitable solution for a given scenario, understanding the implications of prioritizing one machining objective over another.
- Informed Optimization: This approach ensures a more holistic optimization strategy in CNC machining, considering all relevant factors and their interdependencies, rather than focusing on a single objective.
Practical Implications in CNC Machining:
- Comprehensive Optimization Strategy: The use of Pareto-optimal solutions and trade-off analysis in CNC machining leads to a more comprehensive and effective optimization strategy, taking into account the multifaceted nature of machining processes.
- Enhanced Machining Performance: By understanding and applying these concepts, CNC professionals can achieve a better balance of efficiency, quality, and resource utilization, improving overall machining performance.
- Strategic Decision Making: Emphasizing the importance of multi-objective optimization, Pareto-optimal solutions, and trade-off analysis enable CNC professionals to make strategic decisions that align with broader production goals and constraints.
Real-world Case Applications of toolpath optimization
Aerospace and Medical Components with Intricate Features
- Precision and Complexity: In both aerospace and medical industries, components often require extremely high precision and may have intricate features. Advanced toolpath optimization is crucial to meet these stringent requirements, ensuring each part is machined to exact specifications.
- Customized Solutions for Unique Components: Each component in these sectors might have unique geometries and require specialized machining strategies. Optimization algorithms are used to explore various toolpaths, finding the one that best suits the specific contours and features of the part.
- Quality and Performance: The quality of the finished product is paramount in these industries due to the critical nature of the components. Toolpath optimization focuses on factors like minimizing tool wear, ensuring surface finish quality, and maintaining dimensional accuracy.
Impact of Optimization on Aerospace and Medical Manufacturing:
- Efficiency in Complex Machining: With advanced toolpath optimization, complex parts can be machined more efficiently, reducing production time without compromising on quality.
- Enhanced Component Reliability: Optimized toolpaths contribute to the reliability and performance of aerospace and medical components, which is essential given the critical applications they serve.
- Innovative Design Realization: Advanced optimization techniques enable the manufacturing of components with designs that were previously considered too complex or impossible to machine, pushing the boundaries of innovation in these sectors.
Strategic Approach to Manufacturing in High-Precision Industries:
- Iterative Process Improvements: Similar to the concept of generations in genetic algorithms, the toolpath optimization process in aerospace and medical manufacturing involves iterative refinements, continuously enhancing the precision and efficiency of the machining process.
- Adapting to Material and Tool Constraints: Optimization algorithms take into account the unique properties of materials used in aerospace and medical components, as well as the characteristics of the cutting tools, to develop the most effective machining strategy.
- Balancing Speed and Accuracy: In these industries, the optimization process aims to find the perfect balance between machining speed and the accuracy of the final product, ensuring that production timelines are met without sacrificing quality.
Multi-axis Machining and 5-axis Simultaneous Machining
- Handling Complex Geometries: Multi-axis and 5-axis simultaneous machining are essential for manufacturing parts with complex geometries. These advanced techniques allow for machining from virtually any angle, providing the flexibility to create intricate and precise shapes.
- Optimization for Advanced Techniques: Toolpath optimization for multi-axis and 5-axis machining involves exploring various possible toolpaths to utilize the full capabilities of the machines efficiently. This process ensures the most effective approach is chosen for each unique part.
- Reducing Errors and Enhancing Quality: By optimizing toolpaths, the likelihood of errors in machining complex parts is significantly reduced. This leads to improvements in the quality of the finished product, ensuring it meets the required specifications.
Impact of Toolpath Optimization in Advanced Machining:
- Efficiency in Production: Optimized toolpaths lead to more efficient use of multi-axis and 5-axis machines, reducing machining time and increasing throughput.
- Enhanced Capabilities: With optimized toolpaths, CNC machines can achieve higher precision and produce more complex parts, expanding the range of possible applications and designs that can be manufactured.
- Improved Tool Life and Material Usage: Effective toolpath optimization also contributes to better tool life and more efficient material usage, leading to cost savings and reduced waste.
Strategic Implementation in Complex Machining Tasks:
- Iterative Refinement: Similar to the concept of generations in genetic algorithms, the optimization process involves continuous iterations and refinements to find the most efficient path for machining complex parts.
- Customization for Specific Tasks: Each complex machining task may require a unique approach. Optimization algorithms evaluate different strategies based on factors such as machining time, tool wear, and the quality of the finished product, to select the best possible path.
- Balancing Speed and Precision: In multi-axis and 5-axis machining, the goal is to find a balance between the speed of production and the precision of the final component. Toolpath optimization plays a crucial role in achieving this balance, ensuring high-quality output while maintaining efficiency.
Practical Implications in CNC Machining:
- Comprehensive Optimization Strategy: The use of Pareto-optimal solutions and trade-off analysis in CNC machining leads to a more comprehensive and effective optimization strategy, taking into account the multifaceted nature of machining processes.
- Enhanced Machining Performance: By understanding and applying these concepts, CNC professionals can achieve a better balance of efficiency, quality, and resource utilization, improving overall machining performance.
- Strategic Decision Making: Emphasizing the importance of multi-objective optimization, Pareto-optimal solutions, and trade-off analysis enable CNC professionals to make strategic decisions that align with broader production goals and constraints.
Conclusion
In conclusion, the exploration of advanced toolpath optimization techniques, including Genetic Algorithms, Ant Colony Optimization, Particle Swarm Optimization, Deep Learning, and Reinforcement Learning, represents a significant leap forward in the field of CNC machining. By harnessing the power of these sophisticated algorithms, the manufacturing industry is making strides in efficiency, precision, and adaptability.
The practical applications of these techniques in high-precision sectors such as aerospace, automotive, and medical device manufacturing demonstrate their immense value. The ability of these algorithms to handle complex geometries through multi-axis and 5-axis simultaneous machining further underscores their utility in producing intricate and high-quality components.
In essence, the journey through the realms of bio-inspired algorithms and machine learning in CNC machining is a testament to the power of interdisciplinary innovation. It’s an exciting era for manufacturing, where the fusion of technology and traditional practices is paving the way for smarter, more efficient, and more creative solutions in industrial production.
<span data-metadata=""><span data-metadata=""><span data-buffer="">MAAS
Machining As A Service
On-demand CNC Machining Services by Ethereal Machines offers the perfect solution for your CNC machining needs. With secure and confidential processes, you can get an instant quote and access expert advice from their technical team. Whether you need custom CNC machined parts or have a specific project in mind, Ethereal Machines is committed to helping you every step of the way. Try MAAS now and achieve your goals with ease.
Views: 1052